Essential Tips for Safe Welding: From Equipment Usage to Proper PPE and Techniques
The Value of Welding Safety
Welding is a critical process in many industries, but it also comes with serious safety dangers. To prevent harm or death to welders and those nearby, proper safety measures must be in place. Fire and explosions are one of the main risks involved with welding. Welders must ensure their workspace is free of combustible substances and their equipment is in good working order. They must also be aware of electrical shocks and take precautions. Respiratory issues caused by fumes and gases during welding is another concern. Welders should wear the right respirators and work in well-ventilated environments to limit their exposure to these dangerous compounds. Working with large apparatus and equipment also poses a danger. Personal protective equipment (PPE) and proper training can reduce these dangers. Employers must provide the right training and tools to protect the safety of welders and those nearby. Having the appropriate safety equipment is crucial for welding safety, including flame-resistant fabrics, gloves, eye protection, steel-toed boots, and hard caps. Keeping the workspace tidy, well-ventilated, and clutter-free also helps identify potential hazards. Both the employer and the welder must be committed to welding safety and adhere to safety rules to ensure welding is done safely and effectively. In conclusion, welding is essential for constructing and maintaining our civilization, but it is also a dangerous process. Employers and welders can work together to ensure welding is done safely by following proper safety measures.
Upkeep of Welding Equipment for Safe Operation
Maintenance is crucial for the safe use of welding equipment. Although welding is a strong and versatile process used in many sectors, it also poses serious safety hazards. Regular maintenance can help reduce these hazards and protect welders and those nearby from harm or death. Regular inspection is a key component of welding equipment maintenance. Welders should check their tools for wear and tear indicators and make sure all safety measures are operating properly. Regular cleaning and maintenance is also crucial. After each use, welding equipment must be cleaned to remove any residue or debris that can harm it or reduce its efficiency. It's important to check for leaks or damage to hoses, connectors, or other components. Proper storage is also important for maintaining welding equipment for safe use. It should be stored in a dry, cool environment away from direct sunlight to avoid heat and UV ray damage. It must also be stored in a way that protects against falling debris. Proper training is also necessary for maintaining welding equipment for safe operation. Employers must train their welding staff on how to use, maintain, and inspect the equipment safely. Regular planned maintenance is another crucial component. This can include changing worn components, calibrating the machinery, and conducting safety inspections. Employers must establish and follow a maintenance program to ensure the machinery is always in good working order. In conclusion, keeping welding equipment in good condition is essential for its safe use. Proper maintenance can reduce the safety risks associated with welding and protect welders and those nearby from harm or death. Employers and welders must collaborate to make sure the equipment is regularly inspected, cleaned, maintained, stored correctly, and used safely with proper training.
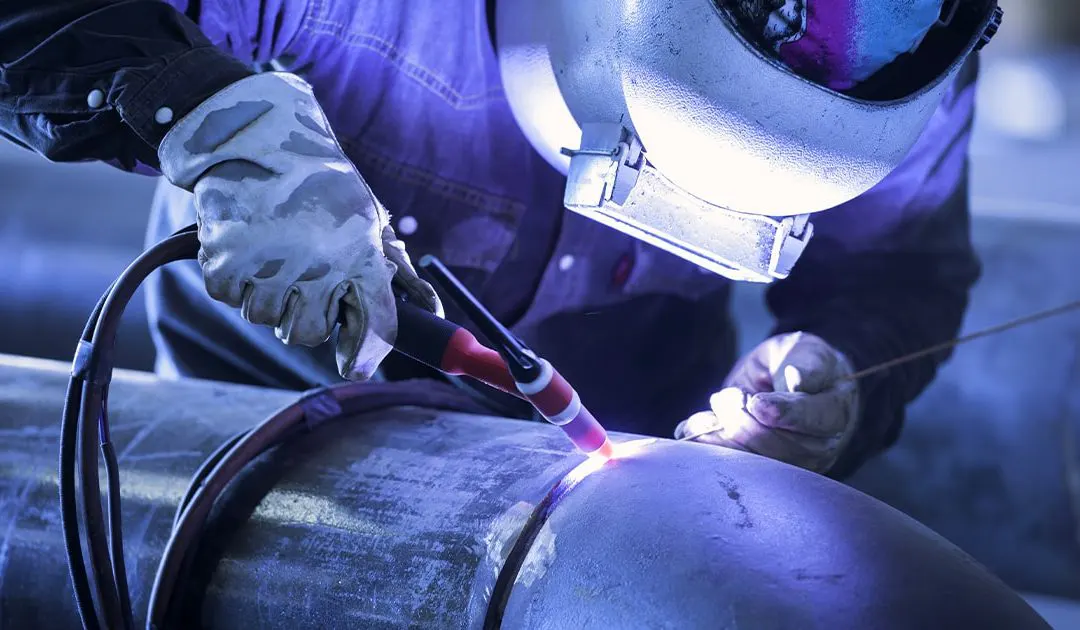
Welders Need This PPE!
Personal Protective Equipment (PPE) is crucial for protecting welders from the risks associated with welding. Although welding is a strong and versatile process used in many sectors, it also poses serious safety hazards. Welders can reduce these hazards and stay safe on the job by using PPE properly. Eye protection is one of the most important PPE for welders. Welders should always wear a face shield or goggles to protect their eyes from the bright light and heat produced by welding, as well as from harmful UV and IR radiation and airborne debris. Gloves are also crucial for protecting welders' hands from heat and sparks. Leather or flame-resistant gloves are the best choice for welding as they provide the required protection while preserving dexterity. A welding jacket or apron and long sleeve shirts and leggings are also important PPE for welders. These clothes, made of flame-resistant fabrics, offer protection from heat and sparks produced during welding. Respirators are necessary to protect welders from the fumes and gases produced during welding. Welders must use a respirator suitable for the type of welding being done as the fumes and gases can harm the respiratory system. Hard helmets and steel-toed boots are also recommended for welders to protect them from crush risks and falling objects. This protective gear will keep them safe from falling objects and heavy machinery. In conclusion, PPE is crucial for protecting welders from the risks associated with welding. Employers must make sure their welding staff have the right PPE and are trained on how to use it. Welders can work effectively and safely by adhering to safety regulations and wearing the proper PPE.
Safety Considerations for Various Welding Methods
Welding joins two or more pieces of material by heating them to their melting point and applying pressure. There are various types of welding, each with its own benefits, drawbacks, and safety considerations. Gas Tungsten Arc Welding (GTAW), also known as Tungsten Inert Gas (TIG) welding, is often used for thin materials and detailed work. The metal is heated with a non-consumable tungsten electrode and filler material is added as needed. Safety considerations include protecting the skin and eyes from heat and light and providing adequate ventilation for poisonous gases. Gas Metal Arc Welding (GMAW), also known as Metal Inert Gas (MIG) welding, uses an inert gas to protect the weld and a consumable wire electrode fed through a gun. This technique is efficient and versatile, often used to weld thicker materials. Safety considerations include protecting the skin and eyes from heat and light and providing adequate ventilation for harmful gases. Shielded Metal Arc Welding (SMAW), also known as Stick welding, uses an electrode covered in flux to form a shield around the weld. Known for its mobility and durability, it is often used to weld heavier materials. Safety considerations include protecting the skin and eyes from heat and light and providing adequate ventilation for harmful gases. Flux-Cored Arc Welding (FCAW) uses a hollow wire electrode filled with flux, similar to GMAW. It is efficient and versatile, often used to weld thicker materials. Safety considerations include protecting the skin and eyes from heat and light and providing adequate ventilation for harmful gases. Submerged Arc Welding (SAW) uses a constantly fed electrode and granular flux to form a shield around the weld. This technique is fast and effective, often used to weld thicker materials. Safety considerations include protecting the skin and eyes from heat and light and providing adequate ventilation for poisonous gases. In conclusion, welding requires proper instruction and safety measures to prevent accidents, injuries, and health risks. It is important to follow all safety regulations, wear the right personal protective equipment (PPE), and maintain adequate ventilation to protect the welder and those around them. Before starting any welding project, it is crucial to understand the pros, cons, and safety issues of each technique.
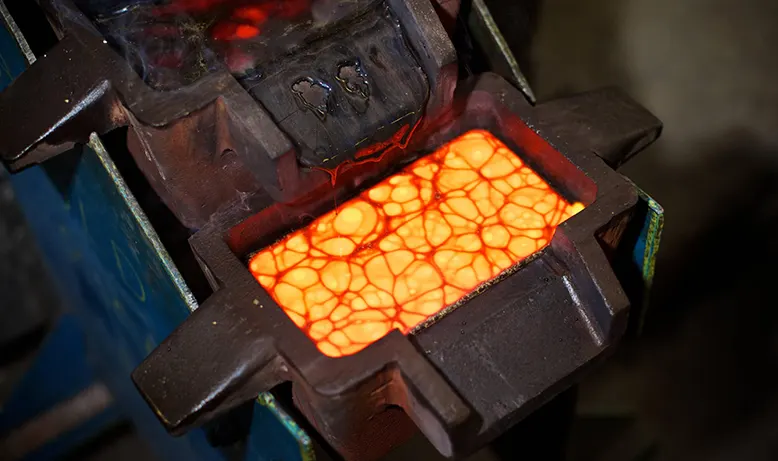
Avoiding and Putting Out Welding Fires
Preventing Welding Fires: Welding requires high heat and sparks, making it crucial to follow safety regulations, keep equipment in good condition, and wear the right personal protective equipment (PPE). Having a fire extinguisher nearby and knowing how to use it is a must in case of a welding fire. Maintaining Equipment: Proper maintenance of welding equipment is crucial to preventing fires. This includes checking for signs of wear and tear, cleaning regularly, and following manufacturer safety guidelines. Adhering to Safety Precautions: Wearing PPE, such as gloves, a fire-resistant jacket, and a welding helmet, and being trained in fire extinguisher use are important steps in preventing fires. It's also important to keep flammable substances and gases away from the welding area. Responding to a Welding Fire: If a welding fire occurs, it's important to act quickly and calmly. Extinguish all sources of ignition and use a fire extinguisher if the fire is small. In case of a major fire, call the fire brigade and evacuate the area immediately. Choosing the Right Fire Extinguisher: Foam extinguishers are effective on class A and B fires, while dry chemical extinguishers can be used on class C electrical equipment fires and class A and B fires. Water extinguishers should not be used on welding fires. Preventing Electrical Arc Fires: Poor maintenance or faulty electrical equipment can cause electrical arc fires. It's important to follow electrical safety requirements and properly maintain electrical systems and equipment to prevent these fires. In Summary: Welding fires can be prevented by following safety regulations, maintaining equipment, and wearing the right PPE. In the event of a welding fire, it's important to act quickly and calmly and have a fire extinguisher nearby. By being aware of potential risks and following safety measures, the likelihood of welding fires can be reduced.
Summary of Important Safety Advice for Welders
Welding Safety Tips for Welders: Wear Proper PPE - Welding helmets, gloves, and fire-resistant jackets protect against heat and sparks. Ensure Adequate Ventilation - Expel hazardous gases with exhaust fans or open windows. Maintain a Clean Workspace - A tidy workspace lowers the risk of accidents and fires. Proper Equipment Maintenance - Regular cleaning and inspection of equipment helps prevent accidents and fires. Have a Fire Extinguisher Ready - Be prepared in case of a welding fire. Recognize Electrical Risks - Electrical arcs can cause electrical fires. Obtain the Right Training - Welding requires knowledge, skills, and training. Know Emergency Protocols - Know what to do in case of an emergency. By following these safety recommendations, welders can reduce their risk of accidents, injuries, and health issues. Welding is a professional activity that requires proper training and understanding to be performed safely. Welders can work safely and effectively by taking the necessary precautions and following safety regulations.