SteelArchives
Metallurgy
04/02/2022
Metallurgy and industry
From iron ore to steel.
Agglomerated iron ore and coke fuel for five ores. In the blast furnace, the coke fuel, which is a type of coal, burns. In this combustion, the iron ore is transformed. At the bottom of the blast furnace, a liquid is formed, the pig iron, which is almost pure iron (3% carbon). The molten iron is collected in an open-topped car that transports it to the converter. Here it is transformed into liquid steel, which is an iron alloy with little carbon (about 0.2 to 0.5%).From scrap to steel
Scrap metal pulled by a magnet is put into an electric furnace: it is melted and transformed into liquid steel.The refining station.
This is used to process the liquid steel to suit industrial needs. For example, by removing more carbon, we obtain a "soft" steel, which is not very resistant but very flexible. If chromium is added, the result is stainless steel.The casting process continues.
Straight from the refining station, the liquid steel is poured into a mould: a bottomless mould with a square or rectangular cross-section that has been cooled down considerably with water. This is why the liquid steel starts to solidify. Then it is pulled down by a set of rollers and, of course, it continues to cool. At the end of the process, as it solidifies in the core, it is cut to the desired lengths. This is how billets are made: these semi-finished products are then transformed into objects. The example of steel illustrates continuous casting, but this technique is also used for aluminium.The foundry.
Here, the metal arrives in a solid state. First, it is melted and prepared: it is mixed with other metals. In this "kitchen", it acquires the properties that are essential for future objects. Then it is cast into moulds in the shape of the future objects to be produced. There are several techniques, including the one described below. To make statues or other art objects, the same moulding techniques are used.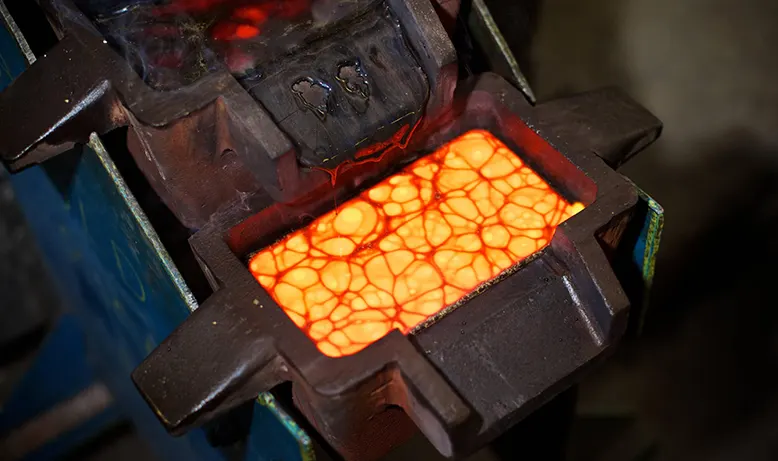